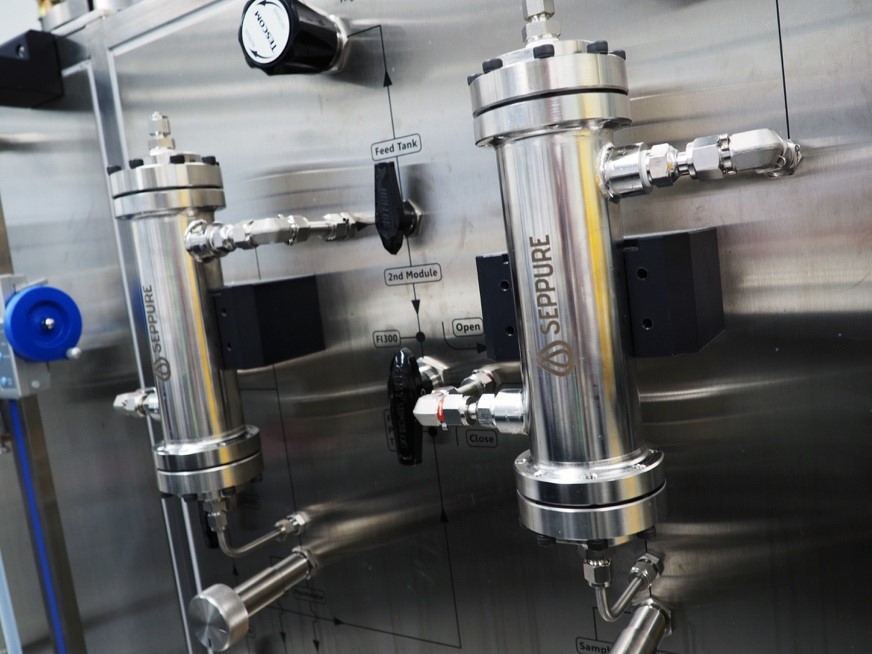
SEPPURE Nanofiltration Technology = Sustainable Separation and Purification
Did you know—the energy required to separate and distil chemical mixtures used in food, medicine and petrochemical production accounts for up to 15% of the world’s entire energy consumption?
Recognising the opportunity to bring about positive change to industries and make a difference to the global climate crisis, Dr Mohammad Farahani set out to find a sustainable chemical separation solution when doing his PhD programme in membrane technology at National University of Singapore.
The Problem with Conventional Chemical Separation Methods
While chemical separation is extensively used across various industries ranging from food to pharmaceutical and petrochemical, conventional methods deployed in the market are costly, energy intensive and unfriendly to the environment.
“For chemicals to separate, they often need to be changed from liquid to gaseous state, then back again. This process not only calls for the use of huge amounts of water, it also emits tonnes of carbon dioxide,” Dr Farahani explained. “That was when I asked the hard question: Can I still get the job done without using any heat?”
Being at the forefront of water innovation, water purification and membrane technologies are not new in Singapore. Membranes for water purification are well established and have been used in the Republic for over 40 years. In comparison, the chemical industry does not have any efficient solution for chemical separation.
“You might think: Why not just use the same membrane used in water separation for chemical separation? But the reality is more complex than that—the same membrane runs the risk of being dissolved or just not performing the job as necessary. Therefore, we cannot just use any membrane—we need a membrane that is chemical resistant,” said Dr Farahani.
Solution and Opportunity
Eventually, Dr Farahani and his team found the solution in a chemical-resistant nanofiltration membrane. With pores smaller than one nanometre, chemical separations can be done at a molecular level without the traditional use of heat. Its high thermal and solvent stability also makes it suitable for a variety of applications with extreme pHs. Furthermore, compared to conventional separation techniques, this technology requires minimal energy—at least 90% less energy consumption.
The implication of the nanofiltration membrane is huge. This sustainable alternative can potentially conserve billions of gallons of water, eliminate millions of tonnes of volatile organic compound emissions and greatly reduce billions of tonnes of carbon dioxide emissions entering the atmosphere every year—globally. In numbers, this translates into approximately US$3 trillion savings on energy expenditures every year.
Adding on, Dr Farahani elaborated, “Our nanofiltration membrane also makes a great business case. To give an example—a low margin industry like vegetable oil refining can easily enjoy increased profit margins of three times or more, working out to about US$7 billion savings a year, industry-wide. And if that is not compelling enough, businesses will love to know that the returns on investment for using our nanofiltration membrane is generally less than a year.”
On the Horizon
The technology is currently being commercialised. It is at the pilot stage of testing with SEPPURE’s early customers. Thus far, data shows that SEPPURE’s technology has desirable performance for industrial applications, and delivers substantial energy and cost savings at reduced greenhouse gas (GHG) emissions.
Beyond which, SEPPURE seeks to roll out the technology globally to different markets and clientele across different industries. Dr Farahani concluded, “Well aligned to the United Nations Sustainable Development Goals (UN SDGs), our technology offers not only environmental benefits, but also economic ones—to businesses, industries and countries.”
Success Stories
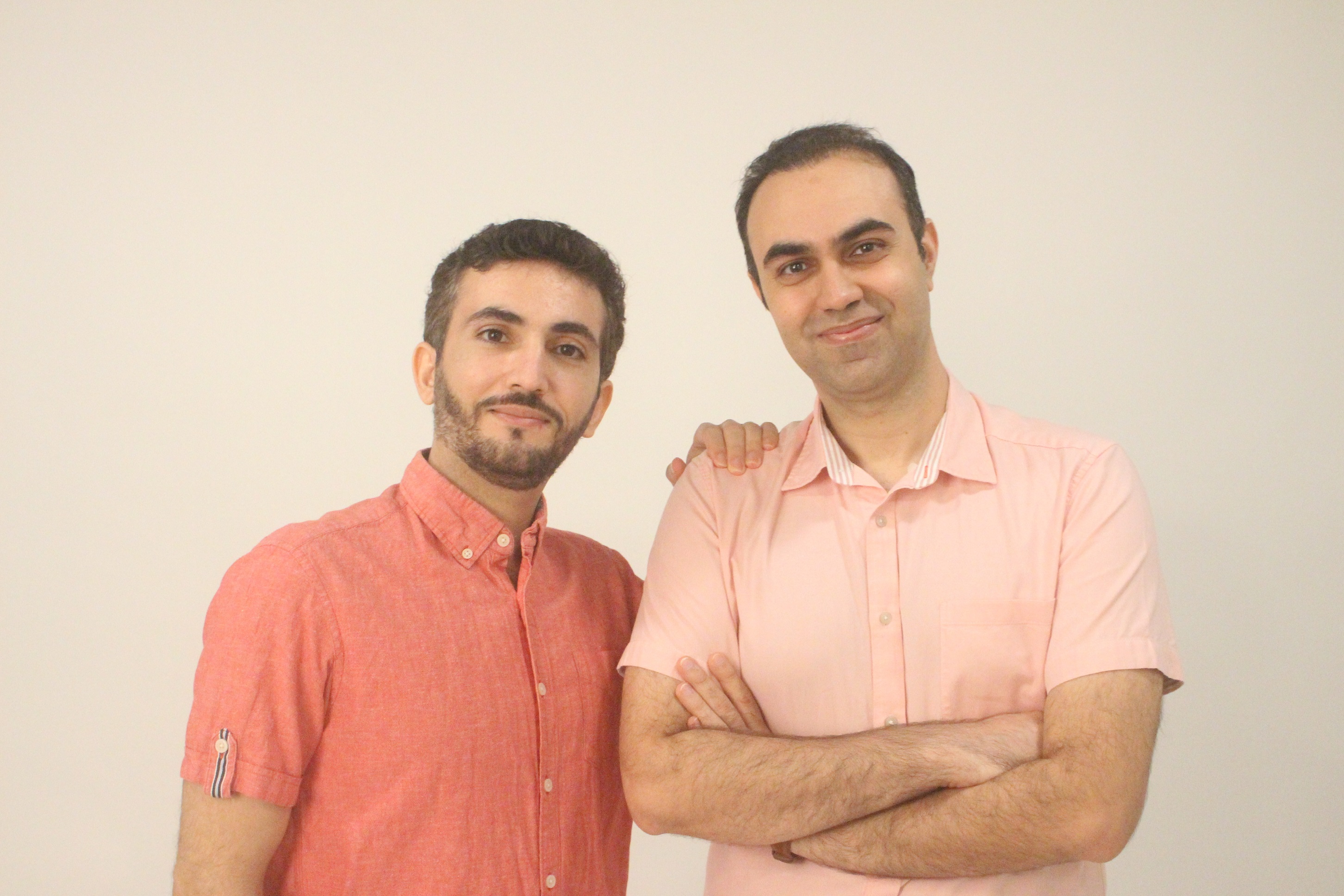
How Allozymes Engineers the Right…
When you eat a slice of cheese, drink a pint of beer or even wear your…
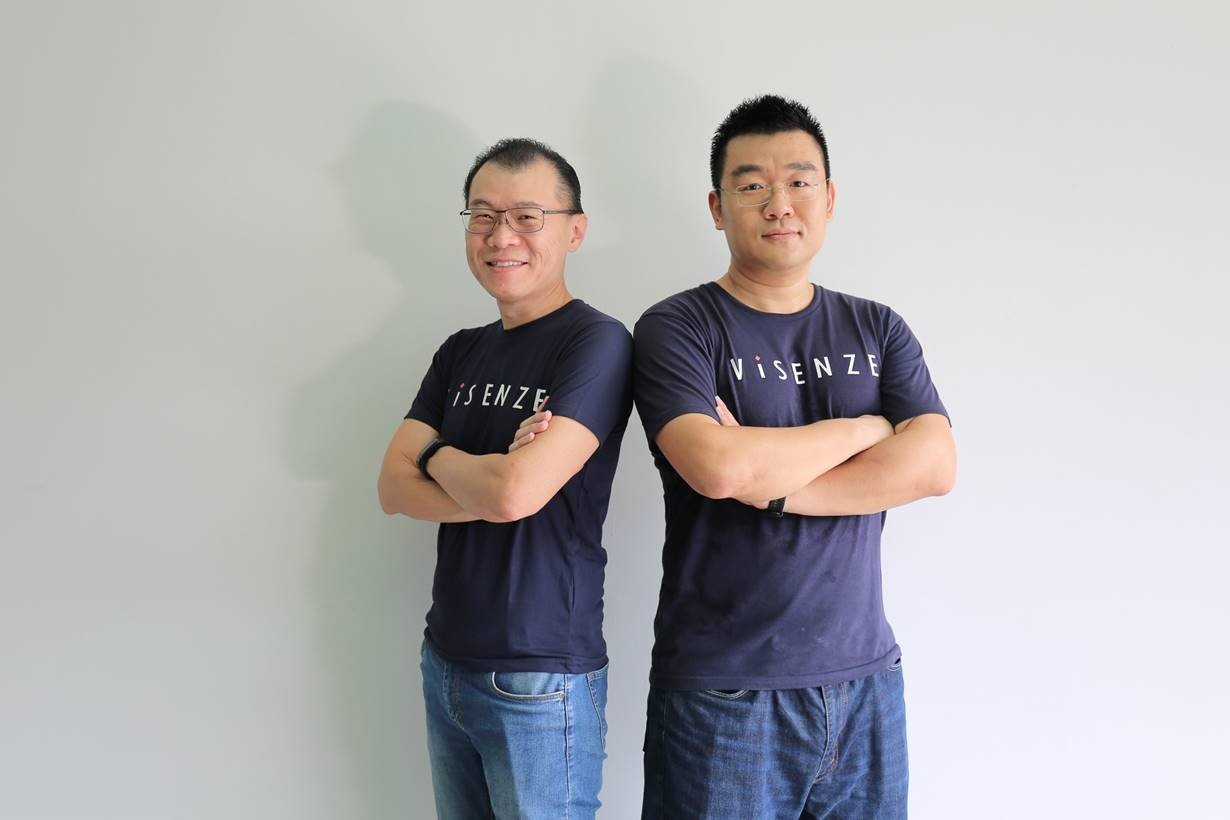
Empowering Search
Imagine walking down the street and spotting someone wearing an incredible…
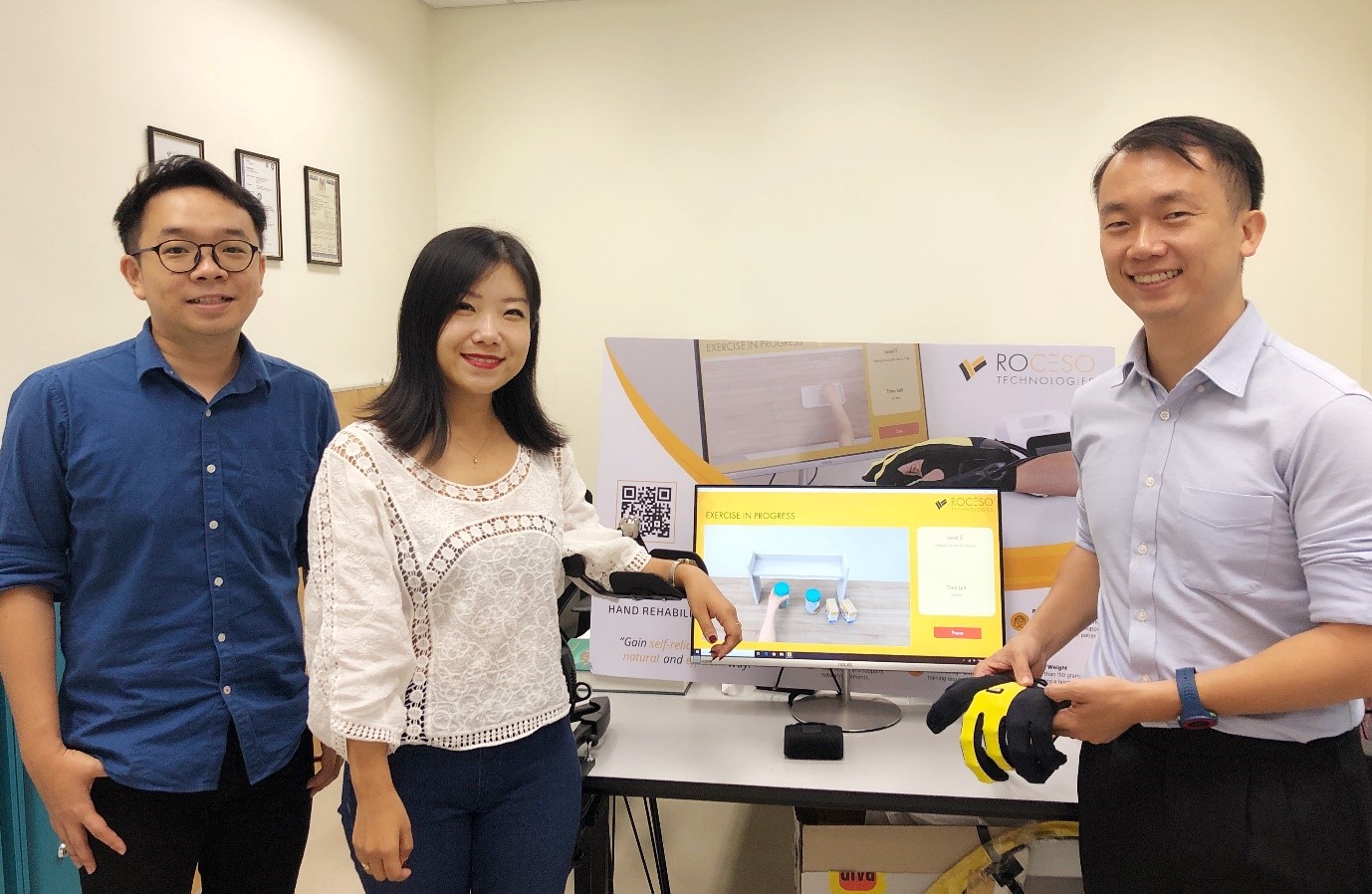
Fits Like a Glove!
Entrepreneurship as a career fits like a glove for Jane Wang, CEO of Roceso…