Precise and Scalable Fabrication of Graphene Foam
Opportunity
Since it was first isolated in 2004, graphene has remained in high demand due to properties such as high thermal and electrical conductivity, and large surface area. Initially isolated in 2D forms (e.g. sheets), the synthesis and use of graphene has extended to 3D forms (e.g. foam)-which are increasingly used for filtration, sensors and energy storage. Besides extensive applications in research, graphene bears potential uses in a wide range of fields such as aerospace, electronics and sports equipment.
The global market for graphene was estimated to be US$620 million in 2020, and expected to grow at a CAGR of 19% to reach US$1,479 million by 2025. However, difficulties in producing 3D graphene foam that retain the high electrical conductivity and flexibility of 2D graphene present continued challenges to market growth.
Technology
This technology is a novel method for fabricating graphene foam via a two-step process.
First, a sacrificial ceramic template is formed using additive manufacturing. The porosity of the ceramic template can be controlled. Its properties can also be fine-tuned. Additionally, complex ceramic template structures can be created.
Next, graphene is deposited on the ceramic template through chemical vapour deposition. The template is then removed using wet etching. If ceramic material such as silica is used, the ceramic template (in this case, porous silica) can be removed under mild conditions, further reducing processing time and complications. What is left after removing the template is a highly porous graphene foam with very large surface area.
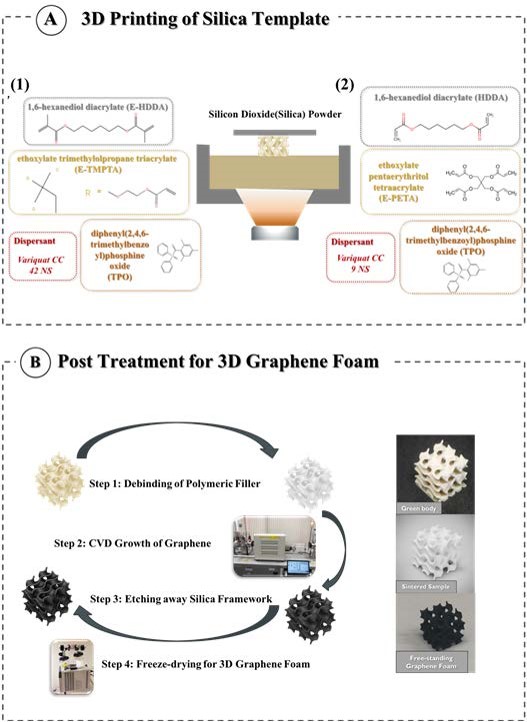